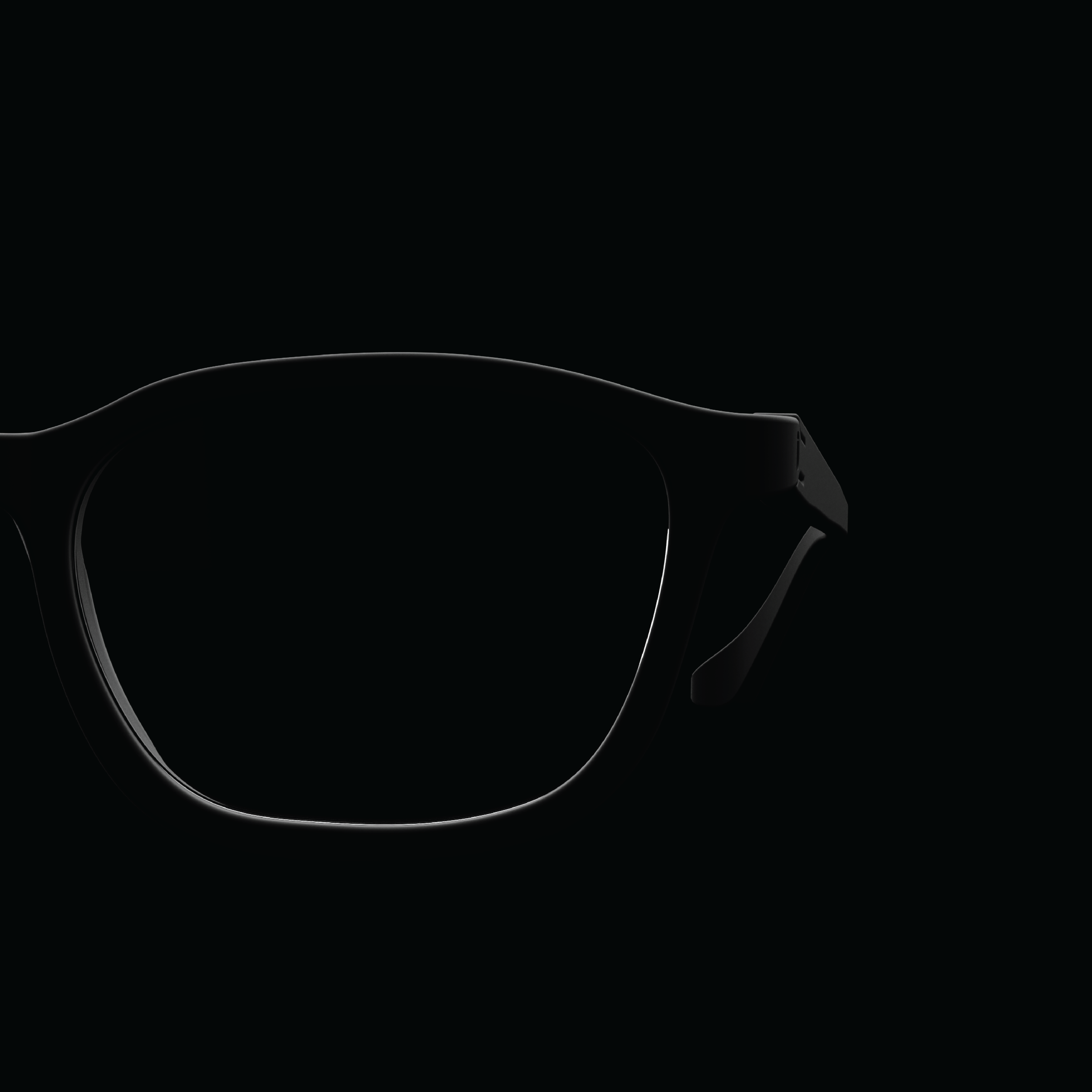
What is the future of Eyecare ?
ID7 is a collaboration within the University of Canberra industrial design cohort of 2021. It aims to answer the question “What is the future of Eyecare”. The team consisted of Alex Khoo, Zac Warren, Eliza Styles, Caitlin Dacey, Hugo Bottrell, Jenn Kang, Lachlan Aboud, Jacky Wei Joon, and myself. We aimed to design glasses frames that could be produced locally and sold directly through the UC Eye Clinic.
Initial Concepts
My Initial concepts involved modifying a CAD model of the glasses frame on a per-customer basis, and then 3D printing the frames to ensure a perfect fit. Initially I had wanted to use cast aluminium sourced from waste cans as the material.
Each team member selected a role they would be responsible for, and I chose ergonomics and fitment as it was the core component of my concepts.
Refinement/Testing
I began working on building a CAD model that would be able to be re-sized and re-shaped to customer demand relatively early in the project. As someone else was responsible for styling I sort of struck out on my own as far as shape goes, which came back to bite me later.
I test-printed a frame derived from this CAD model and the proportions were a bit off but the modelling methodology was sound.
However it was in this section of the project I failed to communicate and work collaboratively with other team members as I did not continue to develop this model as I was expecting the person responsible for styling to reach out to me. I failed to be proactive and work with them.
To prove my value to the team I decided to take on the responsibility for Lens Fitment and finishing of the prototype frames.
Prototyping Display Lenses
-
Lens Profile
The Lens Profile was produced by projecting the outline of the inside of the frames onto a flat plane. This profile was then used to laser cut a mould for vacuum forming
-
Formed Lenses
The Lenses were formed from 1.5mm Acrylic. The mould had 6mm of room for them to gain curvature which was more than enough.
The lenses were then cut using the same toolpath used to produce the mould. -
Initial Lenses
I had initially worried that the lenses I’d made would be too big but the initial batch were 2mm too small in all directions which necessitated a new mould be made.
-
Finished Fitted Lenses
The second revision of lenses fit perfectly to the lens groove in the prototype frames and didn’t have the odd frosting around the edges that the first batch did.
Frame Finishing
-
Raw Frames
The frames were printed using SLA 3D Printing, using Formlabs Tough 1500 resin which aims to simulate the properties of ABS plastic. The 3D Printing process leaves bumps on the surface from the print supports, which have to be removed, and layer lines, which any 3D printing process will have. For user comfort and aesthetic appeal, both of these had to be removed.
-
Sanding
The support material was removed using needle files, then the time consuming process of sanding began. Removing layer lines required quite coarse paper (120 grit). I progressed through the grits up to 1000 grit, wet sanding the whole way.
-
Polishing
After sanding the frames to 1000 grit I polished them with white diamond cutting compound on a calico buffing wheel attached to a dremel.
Final Frame Prototypes
All in all we produced 6 frame prototypes, two “sensible” styles and two more avant-garde styles. The sensible styles were showcased both in natural grey and also dyed black using Vinyl dye. The dye reduces some of the gloss from the polish but that might be a good thing.